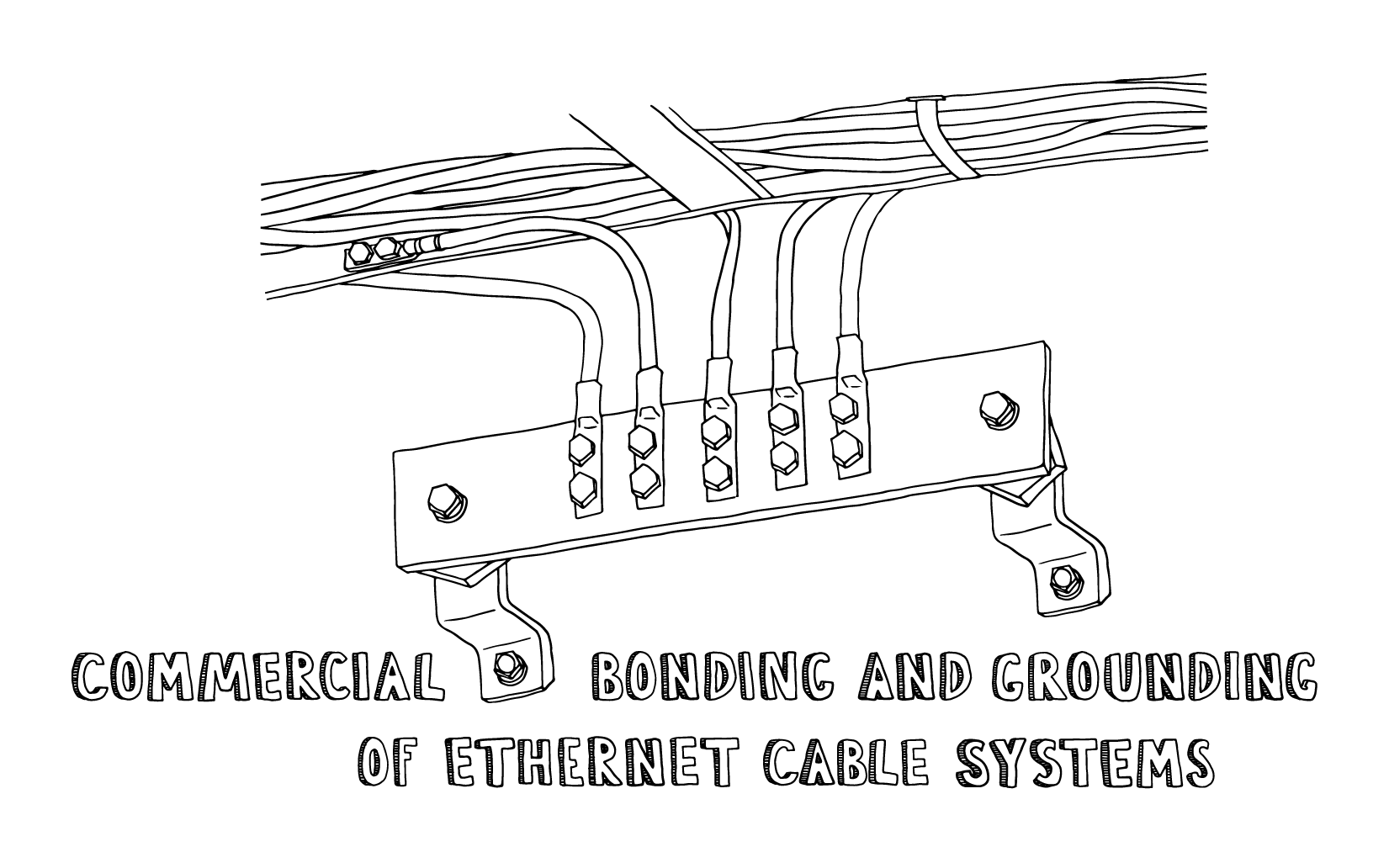
Commercial Bonding and Grounding of Ethernet Cable Systems
Written by Don Schultz, trueCABLE Senior Technical Advisor, Fluke Networks Copper/Fiber CCTT, BICSI INST1, INSTC, INSTF Certified
Bonding and grounding. Of all the subjects that come up when installing Ethernet cable, this one has to be at the top of the list of the items that cause confusion and stress among network cabling installers. It actually is not that complicated when you understand the basic concepts and the differences in terms that are often tossed about. In this blog we will cover these questions and more:
- Are bonding and grounding the same thing?
- What is bonding?
- What is grounding?
- What drives the need for telecommunications bonding and grounding?
- Terms used to describe the telecommunications bonding and grounding infrastructure
- Making bonds and doing it right
- Are there any laws or rules that apply to bonding and grounding?
Further, we will cover a relatively simple commercial bonding and grounding environment with a video. The basics will be covered along with some best practices. Lots of pictures will be provided. A few product recommendations and tips will be provided along the way!
This short video will give an overview of the example system we discuss below in detail. It is designed as a visual and audio aid to supplement this written blog:
Before we begin with our discussion, there are some warnings and disclaimers to cover.

- This blog and associated video is for informational purposes only and is not a step by step bonding and grounding infrastructure installation guide
- Proceed at your own risk
- Always consult a licensed electrician or other qualified professional when designing and building out a bonding and grounding system for your communications cable installation
- Never open an electrical panel (take off the front cover to expose the interior components) unless you are qualified and/or licensed to do so
- Never extend or alter the building AC electrical system unless you are qualified and/or licensed to do so
- Be aware of the electrical codes in your local area or locate someone who is. Codes are actual law, and these codes may or may not be stricter than industry standards and may differ from the NEC/NFPA 70 (National Electrical Code / National Fire Protection Act).
Are Bonding and Grounding the Same Thing?
People get the terms “bonding” and “grounding” all confused and mixed up. We need to separate the two highly related, but essentially different, terms.
But, here is a hint:
Bonding is more of process and result where grounding/earthing is more of a result only. If you are an installer, then you are bonding to ground. If that does not make sense, then I don’t blame you!
What is Bonding?
- EMI/RFI (Electromagnetic and Radio Frequency Interference)
- Electrostatic discharge (ESD)
- Electrical system faults
Bonding the infrastructure for a telecommunication system (telecom) can be achieved in numerous ways, such as copper wire, metallic conduit, busbars, cold water pipes, ladder rack, cable tray, and structural steel. The bonding infrastructure for telecommunication systems is not designed to serve as the intentional path for ground fault currents or other AC electrical system malfunctions! That is the job of the AC electrical system installed by electricians.
Example of bonding an Ethernet cable shield to the connection hardware:

What is Grounding?
Grounding is also referred to as “earthing”. They mean the same thing. Conceptually, grounding is to establish a zero (0) volt reference potential to earth. The ground is between the earth itself and the electrical system inside the building. Its purpose is to provide an intentional path for fault current, and provide a path for ESD to drain off to. The idea is to equalize the earth’s potential with the electrical system potential, and all equipment or enclosures that are part of that system.
Ground rods (called ground electrodes) and GECs (Ground Electrode Conductors) are used for this purpose. There are quite a few ways of installing grounding electrodes and wiring up the associated conductors. The types and ways of installing ground electrodes also vary greatly. Here are some factors that influence whether you have a single ground electrode (rod, plate, etc.) or several all bonded together:
- Size of the electrical system
- Size of the structure
- Design of the structure
- Soil conditions
- Site survey
It should be noted that grounding without proper bonding is similarly useless.
Simple two-rod grounding electrode system with bonding jumper and GEC. The GEC connects to the main AC electrical panel in this case. Image courtesy of BICSI.
Driving Factors Behind Telecommunications Bonding and Grounding
Installation of communications cable (Ethernet included) requires an infrastructure of some kind. In a commercial facility this is likely to be:
- Ladder rack
- Cable tray
- Equipment racks (floor or wall mounted)
- Equipment in those racks
- Metal conduit
Without the above infrastructure, you would have a hard time installing a large amount of Ethernet cable in an organized way!
Given that it is not structurally sound nor safe to use plastic like PVC in a commercial building for supporting all of your cable, ferrous metal (steel) is used instead. Obviously, steel can conduct electricity.
So, bonding to ground the telecommunications system needs to be done for:
- AC electrical system faults
- ESD (electrostatic) discharge
- Electromagnetic induction (EMI/RFI)
- Lightning strikes
The purpose is to ensure human safety and reliability of the telecommunication system by equalizing it all and pathing it to ground. Consider this undesirable situation:
- One metallic object like a rack has a different potential than a conduit due to faulty bonding to ground (or none at all), and then…
- You happen to contact both objects at the same time, possibly becoming the unintentional path for any fault current or ESD. That would be a shocking and possibly lethal experience.
You also want your cable shields for any shielded cable to function properly. Without a bond to ground, shielded cable won’t be shielded any longer and can actually cause a problem with data transmission.
What gets bonded to ground in a telecommunications infrastructure?
- Cable shields
- Any metallic cable support structure*
- Equipment racks and equipment in those racks
- Primary surge protectors and secondary surge protectors
- Power conditioning equipment
*This includes conduits more than 3 feet in length and anything metal that you installed to support or organize your cable except small items like J-hooks.
Who is responsible for the telecommunications bonding infrastructure? You are, as the installer. The electricians should have already designed and installed an AC electrical system that you will eventually bond to. All of your bonding work will lead back to the PBB or Primary busbar, traditionally in the EF or Entrance Facility. Now, we start with some definitions because engineers just love acronyms for everything.
Terms Used to Describe the Telecommunications Bonding and Grounding Infrastructure
In larger telecommunications bonding and grounding systems you see terms like:
- EF = Entrance Facility. This is a term used to describe where all of the OSP (outside plant) cabling comes in for electrical and communications and probably plumbing too. It is that locked room nobody will let some random person into. Usually they have a sign on the door stating HIGH VOLTAGE. This is referred to as the TEF or Telecommunications Entrance Facility in small buildings and may not be co-located with plumbing or electrical systems.
- TR = Telecommunications Room. This is a fancy way of saying the room where your racks and switches are located that radiate all of your Ethernet outward to desks and offices. Usually a TR serves a single floor in a multi-story building with one or more per floor. There can also be multiple TRs on a single story if you have a really big building. If you have a small single story building your TR might also be your ER too. This used to be referred to as “IDF” or “IDF/MDF”. It can come in a lot of different variations depending on your building.

- ER = Equipment Room. This used to be referred to as the “MDF”. This room houses whole building service telecom equipment like a PBX telephone system. The ER can function as a TR, too.
- TBC = Telecommunications Bonding Conductor. This is the single wire that bonds the PBB to the building AC ground system. A registered electrician typically has to hook this wire up. It must be at least as thick as the thickest bonding conductor installed by you elsewhere (TBB conductor gauge or thicker, minimum 6 AWG). It cannot be thinner!
- PBB = Primary busbar. This is a copper bar, 1/4" thick, at least 4” tall (width is variable) where all SBBs (Secondary busbars) connect to. There is usually only one PBB per installation. This busbar serves as the dedicated extension to the building’s AC ground system and is hooked up to the building’s ground system with the TBC. The bar may already be present, or you may need to install it. It all depends on whether you are in a multi-tenant facility or not. The PBB must be mounted on insulators 2” above the wall surface. Think of it as the head of an octopus.
Example of a PBB (also called main busbar). Image courtesy of Harger.
- TBB = Telecommunications Bonding Backbone. This is a minimum 6 AWG coated copper conductor, stranded, and should be green or green with yellow stripes. Used to connect individual SBBs to the single PBB. It is the arms of the octopus.
- SBB = Secondary busbar. This is a smaller PBB. It is the same dimensions as the PBB but only needs to be 2” tall. For every TR there must be a SBB. The SBB serves as the main bonding point to ground in the TR. Each SBB connects back with the TBB to the PBB. All SBBs must be mounted on insulators 2” above the wall surface. Think of it as a baby octopus head at the end of each octopus arm. In other words, one weird looking octopus.
Example of a SBB. Note the bond connection in the third from left position that bonds the ladder rack to the SBB.
2” standoff with insulators must be used on the PBB or SBB. Image courtesy of BICSI.
- BBC = Backbone Bonding Conductor. This wire must be a minimum of 6 AWG stranded coated copper like the TBB, and the same coloring. It equalizes multiple TRs on the same floor. It is also found on the TOP floor and every third floor downward in a large multi-story building. Often the BBC is also bonded to structural steel too. The BBC size must be at equal to the TBB size.
- RBB = Rack busbar. This is a vertical or horizontal copper 1/4” thick busbar attached to an equipment rack with insulators. Although not strictly required, a RBB is the most effective rack bonding method. It is used to bond the rack and equipment in the rack back to the SBB in the TR.** The bar must be offset to allow 3/4” space minimum behind it to make connections. Connections to the RBB should be with 6 AWG stranded coated copper, green color or green with yellow stripe. An exception to this is if the equipment already comes with a pre-attached bond wire (like a shielded patch panel). This manufacturer supplied equipment bond wire should not be less than 12 AWG.
Rack busbar or RBB. Note the bonding conductor that bonds the rack metal to the RBB. The RBB is bonded back to the SBB.
Multiple examples of rack bonding. The first example shows rack bonding without a RBB. The last two examples show horizontal or vertical busbars. Image courtesy of BICSI.
- TEBC = Telecommunications Equipment Bonding Conductor. This conductor is used in the TR and ER. It is used for bonding the racks, conduits, ladder rack, and more to the SBB. This wire must be a minimum of 6 AWG stranded coated copper like the TBB, and the same coloring.
** Some telecommunication equipment does not require, nor has an attachment point for, a bonding conductor. In this case it is acceptable to rely upon the power cord. This includes rack mounted equipment in addition to non rack mount equipment.
Ok, so now that you are familiar with the basic terms let’s see some diagrams:
Placement of the TBC. Remember, only a registered and qualified electrician should make the connection from the PBB or any SBB to the AC electrical system! Image courtesy of BICSI.
Small system example. Image courtesy of BICSI.
Large system example. This is a multi-story building. Image courtesy of BICSI.
Making Bonds and Doing it Right
Using the correct hardware to make the actual connection that establishes an electrical bond is critical. All hardware must be recognized by a NRTL (Nationally Recognized Testing Laboratory)--preferably UL. Here are acceptable physical connection methods:
- Crimping the bond conductor directly to the busbar
- Exothermically welding the bond conductor directly to the busbar
- Listed two hole lug with irreversible mechanical crimp
- Listed two hole exothermic weld lug
Two hole compression lug. These are most commonly used. Image courtesy of Harger.
When attaching a listed two hole lug to a busbar, use a conductive anti-oxidation grease to prevent corrosion. Thinly spread the grease on the busbar mating surface with a brush. Mating surfaces should be free of oxidation or other contaminants.
Image courtesy of Amazon.
Prior to grease application, mating surfaces like busbars can be polished with a green synthetic “scotch” pad. Paint MUST be removed from the bonding surface on rack hardware, rack framing, ladder racks, etc. A wire wheel attachment on a hand drill is ideal for this. Use eye protection!
For plain end metallic conduit used for communications cable over 3 feet long, use screw on or bolt on split collars that have plastic protective sleeves to protect your cable from damage.
Bolt on split collar for conduit. Image courtesy of Harger.
Installed example of a split collar, bonded to the conduit and back to the SBB
If available in the TR or ER, bonds shall be made to:
- Structural steel via exothermic welds
- AC subpanels (let your electrician make the final connection to it)
- Cold water pipes (more likely found in the ER or EF)
That said, never assume that structural steel or cold water pipes have a low resistance path to ground. Two-point resistance testing will have to be performed to be certain it is an effective bond. This becomes critical if the structural steel serves as multiple primary bond points or even takes the place of the TBB. The resistance value must be 0.1 Ω (100 milliohms) or less.
Bonds at the busbar should have a minimum 8” inside bend radius. 10” inside bend radius is preferred. A 90° angle should also be installed as shown.
Bend radius and angle for bonding conductors. Image courtesy of BICSI.
Bonding conductors may need to be sized for length. Per BICSI if no bonding conductor in the telecommunications installation exceeds 100ft then 6 AWG is adequate to equalize all potentials in the cabling system. If bond conductors exceed 100ft then sizing for length will become necessary. TIA has a slightly different take on the matter, and actually gives a table of sizing for length when it comes to the TBB or BBC:
So, who is more correct? I tend to follow the BICSI recommendation of 6 AWG up to 100ft unless there is some reason I should do something differently. I typically use this chart to gauge the TBC (the conductor from the PBB to the AC electrical system ground).
Are There Any Laws or Rules That Apply to Bonding and Grounding?
Yes. Entire books, actually. The better question is what are rules you have to follow and what are best practices that are not necessarily law?
The National Electric Code, which is part of the National Fire Protection Act part 70, sets out guidelines for residential and commercial electrical safety and covers bonding and grounding in detail. Secondarily, bonding and grounding is also part of a standard as set by ANSI/TIA 607-D. Furthermore, BICSI (Building Industry Consulting Service International) has classes and study materials aimed at bonding and grounding best practices. The BICSI guidance is largely based upon the NEC/NFPA 70 and ANSI/TIA 607-D but they do add their own methods and best practices to make this whole subject quite understandable. I strongly recommend the BICSI Installer 1 and Installer 2 series of courses in addition to their specialized bonding and grounding courses.
So, which part of these items should you follow and what is actually law? First, laws are set by local codes. It is entirely possible (but unlikely) that none of these guidelines or standards is actually law in your area. It is also entirely possible that all of the guidelines in the NEC were adopted directly into local law without change by your municipality (very likely). Finally, your local area may have stricter codes than the NEC guidelines and ANSI/TIA standard. You will have to research to find out. Contacting a local code inspector is not a bad idea. It is better to speak and get advice ahead of time rather than risk making a mistake that will get an occupancy permit denied or delayed.
So, there you have it! Commercial bonding and grounding, in depth. Not all topics were covered here. This blog is designed to acquaint you with the topic but is not by any means exhaustive. With that, I will say…
HAPPY NETWORKING!!
trueCABLE presents the information on our website, including the “Cable Academy” blog and live chat support, as a service to our customers and other visitors to our website subject to our website terms and conditions. While the information on this website is about data networking and electrical issues, it is not professional advice and any reliance on such material is at your own risk.