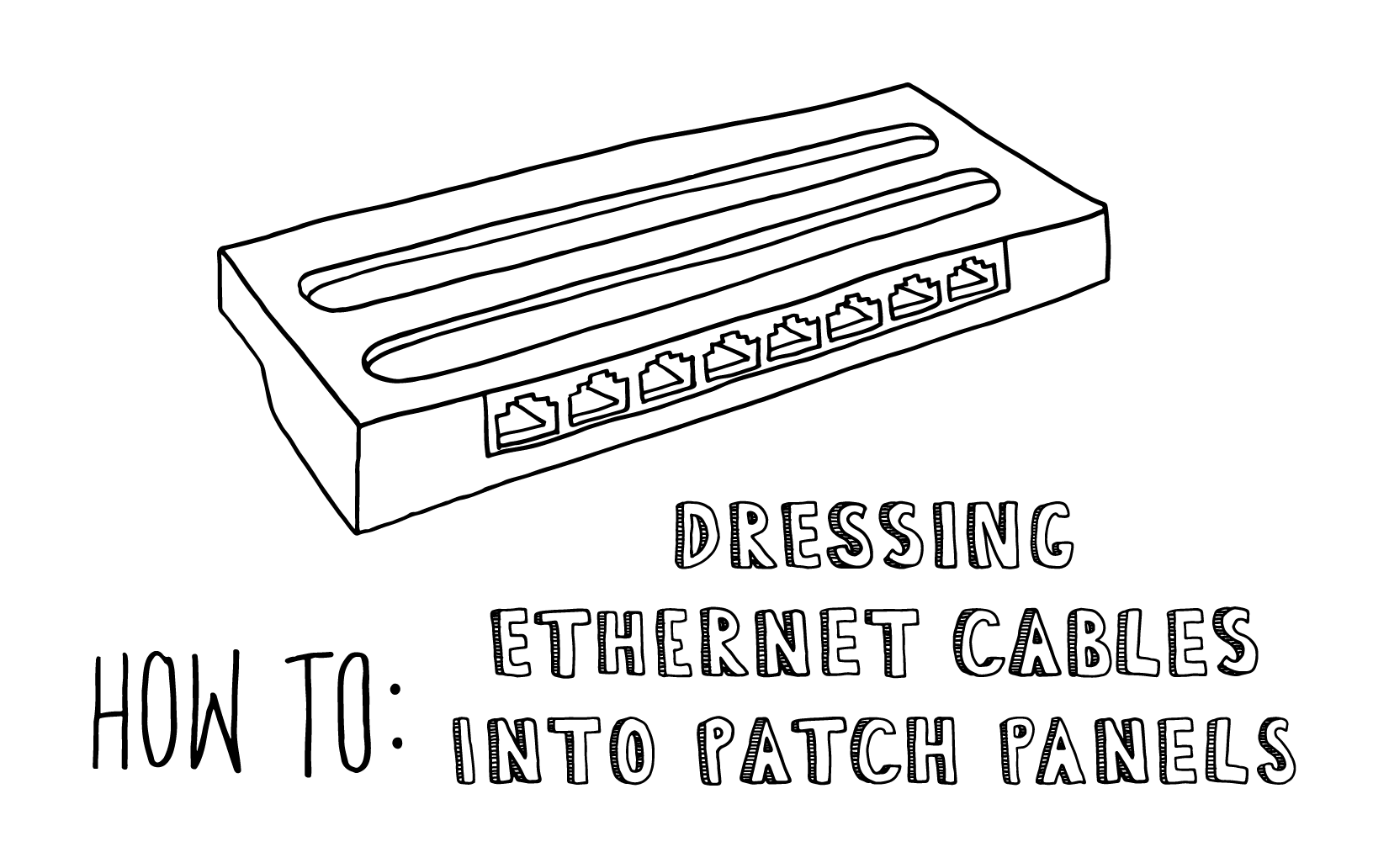
How To: Dressing Ethernet Cables into Patch Panels
Written by Dave Harris, trueCABLE Technical Specialist, BICSI INST1, INSTC Certified
A potentially confusing part of installing an Ethernet structured cabling system is how to handle the “head end” of the installation, which is to say the part that includes the patch panel. The patch panel is typically found in a telecommunications room (TR), in a business, or mounted out sight in a home (enclosure or backboard in the basement, for example). Ethernet cable installations typically involve more than one (sometimes thousands) of cable all running back to this central place. The result can resemble a spaghetti monster. In order to maintain your sanity (and the sanity of the next person who has to work on the installation) this whole thing needs to be labeled, organized, and set up for success. How should this be done? How do you keep track of what cable is what? Do I need slack (extra cable) and how much? Are there any industry guidelines for how this is done? Well, get your cup of coffee ready! We are going to cover some basic SCS (structured cabling system) concepts to set a baseline of how this is done, plus provide some advice for residential and commercial situations. Oh, there will be pictures!
Why a Patch Panel?
When customers come to us with questions about designing an Ethernet cable installation for their home or small business, we advise them that the best performance, reliability, and flexibility result from installations consisting of “permanent links.” Cables are routed through walls and ceilings so that they are concealed from view, and also protected from physical damage. The patch panel organizes those permanent links and can greatly increase performance and stability.

Simple representation of a permanent link in a jack-to-jack configuration. This is just a diagram. The key point is that permanent links end up with “female” connectors. The blue cable is solid copper Ethernet.
Terms You Need to Know
Patch panel: Place(s) where you terminate and organize all of the structured solid copper cabling that is running through the walls, ceiling, floor, etc. Think of it as the head of an Octopus. They come in various flavors and sizes.
Permanent link: Solid copper Cat5e, Cat6, Cat6A, or Cat8 Ethernet cable that is terminated to a patch panel on one end and directly to a keystone jack outlet on the other for residential or smaller commercial installations. Larger commercial installations may also have patch panel to patch panel permanent links between telecommunications rooms, known as back bones. Permanent links have a maximum run distance of 295 feet (100 meters). Keep in mind that permanent links are subject to length derating if temperatures exceed 68℉. For more information on length limitations see Temperature's Effect on Ethernet Cable Length.
Patch cord: Patch cords, also known as patch cables, are short factory pre-made cable with 8P8C (aka RJ45) connectors already installed on the ends. Patch cords are meant to be used from the patch panel to your Ethernet switch(s) on the “head end” and also used from the keystone in the wall to your destination device on the remote end. The patch cords you select should match the Category of the permanent links you have installed, and should also be shielded if your permanent links are shielded. Keep in mind that the gauge of the stranded patch cords you use can and will affect your overall channel length, just like temperature can. The thinner the gauge of the patch cord, the less length you can use. Please see Calculating Ethernet Cable Overall Channel Length for Success.
Keystone jack: Keystone jacks are used to terminate solid copper Ethernet cable and can be used at both ends of your installation. A good example is a keystone jack patch panel and then keystones mounted in wall plates in your remote rooms/offices. Keystone jacks are far superior to RJ45 plugs due to their Category rating and much more secure mechanical design. Keystone jacks provide a “female” port to plug into.
RJ45: RJ45s are actually 8P8C (8 position, 8 contact) “male” modular plug connectors that should already be installed onto both ends of factory pre-made patch cords. It is strongly recommended to not use hand terminated RJ45s throughout your installation, especially with solid copper Ethernet. If you do need to put on a male connector, please consider using a Field Termination Plug instead. In some cases, you MUST put on a RJ45. It happens. In that case, it would be at the device end for a PoE access point or camera. The other end of the cable should still be a keystone termination. Keep in mind that RJ45 selection is critical. Please see Selecting the Correct RJ45 Connector.
Service Loop or Service Slack: For residential installers, pull approximately seven additional feet more than you need to store as extra cable above your patch panel for adds/changes/moves/mistakes. Two feet will be removed during the dressing and termination process, leaving five feet of actual extra cable. For commercial installations, TIA recommends pulling enough additional cable to reach from one side of the TR to the other plus the height of the TR. How much additional cable that is depends on your TR size. If we are talking about a typical 16ft x 16ft TR, then this would be 26 feet of service slack stored on the ladder rack above your patch panel(s). Remember to not pull so much service slack that you violate the Ethernet cable length limitations! Each install is different, so common sense and planning all play a role.
Here is a graphic that will help demonstrate some of the terms:

At the device end, the keystone jacks are supported by faceplates mounted to the walls in the workspaces. Instructions for mounting a jack and faceplate in a wall are provided in our Cable Academy blog, “How Do You Install a Keystone Jack Into a Wall”?
Let’s Get Started!
In this article, we’ll explore solutions for finishing the other ends of the permanent links, at a patch panel located close to the switch (or router). If there are only a few cable runs (say up to three or four), the keystone jacks can be mounted in the wall using a multi-port faceplate, with patch cords finishing the connections to the switch or router. You are still using permanent links, and the multi-port faceplate is functioning as your patch panel.
If more than a few runs are installed, then the keystone jacks should be mounted in a patch panel, with patch cords finishing the connections to the switch. If you are running shielded cable, then a patch panel is necessary no matter how many cables are installed. This is because the cable shields must be grounded. A patch panel made for shielded keystone jacks provides a bonding wire for this purpose. It is very difficult to achieve this connection to ground, especially in a residential structure, without using a shielded patch panel.

A shielded patch panel with openings for keystone jacks. This panel is designed to be mounted in a telecommunications rack. Service is shown to good effect!

Note the green wire for bonding the panel and fitted keystone jacks to ground.

Some ideas for grounding shielded cable can be found in our blog, "Residential Bonding and Grounding of Shielded Ethernet Cable Systems."


Not all patch panels are made to accommodate keystone jacks. Some patch panels already have jacks permanently installed, with connections made by “punching down” the conductors directly to IDC contacts located on the rear of the patch panel. In commercial settings with a lot of cable runs, punch-down patch panels can save installation time. Skill and experience are required to terminate punch-down patch panels while avoiding signal loss. Because of this, and the ability of the keystone patch panels to accommodate a variety of different types of modules, punch-down patch panels are being deployed in fewer and fewer new installations. See Punch Down, Feed-Through, and Toolless Keystone Ethernet Patch Panels Explained for the different types of patch panels in detail!



Mounting the Patch Panel
If you are installing a patch panel into a residence or small business, It is often more efficient to mount the patch panel on a wall so that purchase and installation of a rack or cabinet is not necessary. When mounting a patch panel or any other equipment on a wall, it is best to mount a plywood back board first. Use ¾ inch plywood, and size the board to allow mounting of future devices and cable service loops. Once the back board is mounted on the wall, equipment can be screwed directly to the board, eliminating the need for wall anchors (unless they were needed to mount the board). It is normally a good idea to paint the backboard, just so it looks better.
In commercial installations, backboards are usually required on the walls of telecommunications rooms. These backboards are required to be ¾ inch, AC grade, fire-retardant plywood. They are often required to be painted with two coats of fire-retardant paint, and you may not be able to paint over the fire-retardant stamp the manufacturer put on the back board. Your local Code inspector will let you know what rules have to be followed. The board(s) should be mounted with the bottom edge eight inches from the floor. Check out the video below for a more in-depth demonstration of this process.
Alternatively, you can see an example of what this looks like within the photo below.

Example of a backboard in a small business setting. This is another example of an older installation observed during a network survey. There is a patch panel located near the center of the photo. Note that there are several service loops coiled and mounted on the board. The cable runs to the patch panel are the blue Ethernet cables routed down the right-hand side of the board and into the rear of the panel. It’s good that they bundled the cable neatly and followed an unobstructed route. It’s bad that they used zip ties to bundle their cable. Don’t do it! Use hook and loop straps to bundle the cable. The straps can then be mounted to the board.
Routing and Dressing Permanent Link Cables - Residential
At the device end of your permanent link, the cable is terminated to a keystone jack and installed into a wall faceplate. Leave a small service loop, about 12-18 inches, either coiled in the wall box, or above the ceiling. It’s best for these to be hidden to maintain the design and décor of the room. This is pretty much the same for both commercial and residential installations. However, a commercial installation might specify a longer service loop in the ceiling above the outlet. See how it's done in the video below!
At the service end (head-end) of your permanent link (where the patch panel is), the cable is either punched down to the patch panel, or terminated to keystone jacks for installation into a keystone patch panel. Always leave a “service loop,” which is a coiled up length of slack cable in case the run ever needs to be serviced. You don’t want to run short of cable if you have to re-terminate or move the patch panel in the future.
In the home or small business installation, you can bring the cables in through an opening in the wall or ceiling. Bundle the cables together and route them down or across the board toward the location of the patch panel. Use hook and loop straps to bundle the cable–not plastic zip ties. Leave a small portion of some of the straps unwound, so you can mount the strap to the backboard with a screw..
Before you cut the cables to length, remember the following:
- Leave a five foot service loop for each permanent link cable. The service loops can be coiled and attached to the board using hook and loop straps. This means to pull seven more feet than you need at the patch panel side. Two feet will be used for dressing and termination. The remaining five feet will be the actual service loop stored.
- There should be an identifying mark on both ends of each cable. Make sure that you remark the cable at a spot where it will not be cut off and lost.
- If you have a patch panel that is hinged so it can swing out from the wall, make sure to leave the cables long enough to allow the panel to swing freely. Terminate the patch panel with the hinge open, making sure that it can also be closed.
If you are using a punch-down patch panel, bring the cable up to the connectors for its destination port on the panel. Mark the position on the cable where the cable jacket will be scored and removed. Before making any cuts, remark the cable with its identifier so it will not be lost. Punch down the conductors to the panel, following either the 568A or 568B color sequence. Do each cable one-at-a-time, so you can make sure that each cable ends up at the optimum length for a tidy installation.
If you are using a keystone patch panel with snap-in keystone jacks, the same procedure applies with just a couple of differences. The cables can actually be routed through the keystone holes before termination to help avoid tangles. Don’t mark the cable jacket to be snapped open right at the position of the patch panel. Instead, subtract off about an inch to allow for the depth of the jack. When you install the jack into the patch panel, insert the bottom of the jack first. With the bottom cleat in place, rotate the jack upwards so that the snap latch on top of the jack snaps into the panel. Do these one-at-a-time so slack is minimized and the cables look nice and orderly behind the patch panel. Finally, label the patch panel, wall faceplate and each end of each cable with a unique identifier. You can see an example of this process in the video below.
Routing and Dressing Permanent Link Cables - Commercial
For a commercial installation, there are more requirements and more challenges. There might be multiple patch panels and hundreds of permanent link cable runs. Imagine the work involved to bundle the cables neatly while making sure that each run ends up at its predetermined patch panel port. Tangles are a constant threat. Every run will have a service loop that must be stored someplace. Often they are neatly arranged on ladder racks or in cable trays above the racks. Finally, a commercial installation might require that you employ the ANSI/TIA 606-D standard for complete labeling of the cables. More commonly your customer will dictate the labeling scheme, but rest assured you will need to follow some sort of labeling scheme. If in doubt, always ask. This is one area where you don’t want confusion as having to tone and trace or otherwise run down what is what in a commercial installation may take hundreds of hours.
Each site is different, and installations such as these require technicians with years of training and experience. For that reason, a full description of cable routing and dressing in a commercial installation is beyond the scope of this meager blog.
So, there you have it! This is an overview of the process of working with patch panels. Nothing will beat practical experience. Each time you work with a structured cabling system you will have a new and unique project on your hands. Furthermore, we suggest you seek out formal BICSI Installer training if you are in the field of installing communications cable for a living. Suggested courses are BICSI INST1 and BICSI INSTC. Please visit www.bicsi.org for more information!
HAPPY NETWORKING!!!
trueCABLE presents the information on our website, including the “Cable Academy” blog and live chat support, as a service to our customers and other visitors to our website subject to our website terms and conditions. While the information on this website is about data networking and electrical issues, it is not professional advice and any reliance on such material is at your own risk.
Long time question… most patch panels don't seem to offer space to write/label WHERE the cable run goes to—what room.
How/where do you identify where the cable run goes to?